Successful Applications
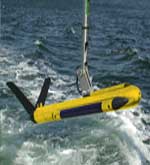
Sonar is an acronym for sound navigation and ranging and allows one to “see” through the water using acoustics. Sonar has many uses in navigation, communication and detection. Active sonar can be used to detect submarines too quiet to be located with passive sonar. Other active sonar systems are used to detect large marine mammals in commercial shipping lanes or in high sound pressure zones such as those used for military exercises.
One of Vicor’s customers specializes in rapid prototyping of harsh environment instrumentation and ocean-acoustic research. Their expertise in quantifying noise and vibration measurement has been applied in diverse commercial and government programs. A recent project involved the development of an enhanced active sonar system for harbor defense.
The sonar system is an underwater cylinder with attached hydrophone transducers. The system transmits a signal and waits to receive a reflected signal in response. The incoming signals are interpreted to identify the object or intruder, i.e. a swimmer, whale or underwater vehicle. This underwater detection system has to be as small and unobtrusive and function at a low internal temperature. Most importantly, the system must operate with high reliability.
The customer chose a V•I Chip solution for the high efficiency, low noise and small size attributes that are critical to this application.
The power requirement for the sonar system is 1 kW. The small, low profile PRMs and VTMs are connected in a high-power parallel array that provides control of isolated Point of Load voltages of 48, ±15, ±12, and 5 V. Another requirement of the design is to control the internal temperature in the system. The compact structure of the system does not allow for significant internal air circulation. Moving heat out of the system and into water was a priority. The very low heat dissipation of the V•I Chip modules is an advantage.
In this sonar application, signals are transmitted at a very low frequency. Received signals are amplified, so any noise interference is also amplified. During the process of transmit and receive, conventional switching power supplies operate at no load and switch in the same frequency band as the system, making noise an issue. The PRM and VTM modules array operate on a fixed higher frequency that switches above the target band, so there is no noise interference.
MIL-COTS VIPAC Powers a Helicopter-Borne Laser Diode Countermeasure System
A laser diode is a semiconductor similar to that found in a light-emitting diode. They are numerically the most common type of laser, suitable for a wide range of applications, including incorporating them into tactical vehicles and aircraft for self–protection and missile defense. Compact, high–efficiency lasers are critical for airborne electro-optic countermeasures, and laser diodes provide the requisite compact size, ruggedness, and efficiency.
Our customer provides solutions for government agencies and defense including involving active and passive signal processing systems. One, a laser diode countermeasure system for Army helicopters, is designed in two parts, the command and control board and the laser diode driver board. MIL-COTS VIPACs are used for both parts. The command and control card, one per system, has a VIPAC with three modules, a 15 V, 5 V, and a 24 V brick, trimmable to 15 V, 7 V, and 5 V. The laser driver card, two in each system for redundancy, has a VIPAC with one 24 V brick and a VIPAC with one 15 V brick.
The MIL-COTS VIPAC family of power systems is a class of user-defined, modular power solutions for the most demanding military applications. They incorporate preassembled and tested front ends to provide input transient protection perMIL-STD-704E/F (M-FIAM5B), MIL-STD-704A/E/F, and MIL-STD-1275A/B/D (M-FIAM9). They also compliant to MIL-STD-810F for vibration and shock. Incidentally, the wide trim range of Vicor modules can provide operating voltages as low as 500 mV.
Multiple Vicor Power Solutions Help Preserve Aviation Security
After September 11, 2001, airport and airline security assumed a much higher level of attention with the airlines, the government, and the public. Within weeks, the Department of Homeland Security was forming. Before the year was out, the TSA (Transportation Security Administration) was formed (later absorbed into Homeland Security), carry-on items were restricted, security on the aircraft was improved, ID checks were implemented, and programs for effective screening systems were underway to name a few.
Effective screening systems to detect threats are now on line that minimize passenger waiting times and avoid large and expensive solutions with increasingly better detection solutions on the way.
Our customer, a maker of explosive detection systems, offers systems that inspect all checked baggage for explosives. These systems are small, inexpensive, and satisfy the guidelines of their main customer, the TSA, including, for example, the California earthquake vibration specification test.
Various Vicor modules are used in a number of different scanning products. VIPAC AC-DC power systems, for example, power fans, and FlatPac configurable AC-DC power systems are used to power arrays and circuit cards. MegaPac, a family of user- and field-configurable power supplies, powers the tank of a number of scanners. Scanner power requirements are typically single phase, 200 to 240 Vac, 50/60 Hz, 20 to 30 Amps.
Vicor configurable power supplies were appealing for these applications because they are compact and reliable. Because each individual power supply is based on a standard, modular design, any model variation is quickly available, some even configurable in the field.
Superior EMI / EMC Filtering for Flight Instrumentation
A flight management system (FMS) is a fundamental part of a modern aircraft. It controls the navigation, holds the flight plan, and logs important data needed to ensure the scheduling of routine maintenance. It uses various sensors and global positioning equipment to determine the position, altitude and speed of the aircraft, and given the position and the flight plan, the FMS also helps guide the aircraft to the desired destination. The FMS is normally controlled through a small on-board computer which will output a display of the electronic flight instrument system. The modern FMS was introduced on the Boeing 767, though earlier navigation computers did exist. Now, they can be found on aircraft as small as the Cessna 172.
Flight management systems and other peripheral devices such as radar, terrain awareness, and data loggers, typically need to be able to operate from a noisy 24 Vdc voltage source that has been down-converted from the AC that is generated by the plane’s engines. A typical FMS device often has low steady state current requirements, at 7 A or less, but could have peak requirements up to 10 A or more. For these applications Picor’s QPI Active input filters can filter the EMI and support requirements up to 14 A.
In addition to aircraft EMI requirements, cockpit displays may require a low ripple power source, with noise levels <10 mV p-p. Power to displays is less than 30 V, and current levels can be as high as 10 A. Picor QPO and uRAM active ripple attenuators can support requirements up to 30 A.
Since cockpit space is tight and low-noise performance is critical, active filters provide unique value by combining superior noise attenuation and a compact package size. Both the QPI input filters and QPO output ripple attenuators come in a standard
25 mm x 25 mm x 12.5 mm low-profile LGA package.
Picor Active Filters Overcome Noise – Challenges for Helicopter Displays
Picor’s Active output filters have been designed into a wide variety of display applications from Medical X-ray and MRI to commercial and military aircraft displays. Video designers are replacing bulky cathode-ray tube displays with much thinner and space-efficient liquid crystal (LCD) and light emitting diode (LED) displays. For new applications, some are specifying displays as small as 2.5in across to make the most of the cockpit space. These changes create new demands on the power source and on the management of the Periodic and Random Disturbances (PARD), the noise on the input power to the display.
Picor active ripple attenuators meet the stringent requirements of, for one example, the US Department of Defense DO160 standard and provided higher attenuation than passive filters in a much smaller space. Picor’s QPO active filters provide output ripple and noise attenuation of more than 30 dB from 1 kHz to 500 kHz and more than 20 dB in the 50 Hz to 500 Hz range. The QPO features a standard 25 mm x 25 mm form-factor. A single module replaces several bulky passive components and provides better results. For higher power the uRAM active filter can provide >40dB attenuation from a 60 Hz to 1 MHz, up to 30A, in a 57.9mm x 36.8 mm form-factor.
Able to support load currents up to 30A, these small filter modules can handle a wide voltage range from 0.3 V to 30 V DC, as well as providing better noise attenuation than a bulky network of external passive components. The QPO and uRAM closed-loop architectures improve transient response – vital for modern embedded computers and displays – and ensure quiet point-of-load attenuation. The efficiency of the active filters can be as high 99%; the uRAM also includes built-in ORing functionality.
Vicor Applications Engineers – Solve Problems Face to Face and in Video
Electromagnetic noise is pervasive. It is the result of electric currents, magnetic fields, and electromagnetic fields. Practically, that means noise is created by such natural phenomena as lightning and solar flares, and manmade electrical or electronic devices like radio transmitters and switching power supplies. In the context of power system design, noise ― commonly referred to as electromagnetic interference (EMI) or radio frequency interference (RFI) ― appears as unwanted currents. These unwanted currents degrade the performance of any susceptible device. Electromagnetic Compatibility (EMC) is the ability of the source and the receptor to operate in a given electromagnetic environment.
One of Vicor customers is a design house mainly for MIL ground and flight applications, which includes products that suppress or eliminate radio frequency noise and electromagnetic interference. In addition to using Vicor products (all five of their current platforms use Vicor products), a long-time working relationship exists between their designers and Vicor application engineers.
In a recent encounter, involving a design in which they wanted to implement Inmate sockets, the designer mentioned a requirement for extremely low output ripple and asked about using some discrete components (LC) at the output to reduce the ripple. The apps engineer showed him a sample of a Picor QPO output ripple attenuator and told him that it was an active filter specifically designed to reduce power supply output ripple and periodic and random deviation (PARD) noise over 30 dB from 1 kHz to 500 kHz. He immediately ordered a QPO evaluation board. The designer also mentioned watching the video on output ripple reduction and that he was very pleased with the information presented.
QPI Active Filtering for Improved EMI performance – for Thermal Imaging Camera (EN60945 Compliant)
Modern thermal imaging technology is capable of both sensing infrared radiation and then converting the thermal energy into an image for a video output. The video can then be used to help pilots and drivers navigate and detect objects in the dark, and in fog, or detect warm objects against a cooler background when it is completely dark (such as a cloudy, moonless night). Thermal imaging is often used in naval vessels, fixed-wing aircraft, helicopters, and armored fighting vehicles. In warfare thermal imaging technology provides three significant advantages. First, the imager itself is nearly impossible for the enemy to detect, as it detects energy that’s already there, and doesn’t have to send out any energy of its own. Second, it sees heat, which is hard to camouflage. Thirdly, thermal imaging systems can see through smoke, fog, haze, and other atmospheric obscurants better than a visible light camera can.
A Picor customer was designing a thermal imaging device for video over IP application. And due to the nature of the application, it needed to comply with EN60945 EMI limits, which is a compliance standard which applies to Maritime Navigation and Radio Communication Equipment and Systems. The compliance limit on this standard is 10dB lower than the Class B limit for frequencies above 5 MHz, which creates a greater challenge for an EMI designer.
The application required a filter compatible with a 24 V input converter, at a power level of less than 150 W. For this application, the designer was looking to replace a passive discrete design with a Picor QPI-3LZ filter. The customer requested a QPI evaluation board which allowed them to evaluate the performance of the filter in a matter of days rather than weeks. The evaluation demonstrated that the QPI filter was able to provide a greater margin of compliance than the passive design both at higher frequencies, as well as the lower frequencies. Another important factor in selecting the QPI filter was the size. The small size (1″ x 1″) of the QPI filter made it possible to easily fit the device within the same area that had previously been allocated for a passive design.
Battery Charger for a Military/Ruggedized UPS System
Uninterruptible power supplies (UPS) supply power from a separate source, typically a battery, when utility power is not available. A UPS provides uninterrupted power to equipment, typically for 5–15 minutes until an auxiliary power supply can be turned on, utility power restored, or equipment safely shut down. While not limited to safeguarding any particular type of equipment, a UPS is typically used to protect computers, data centers, telecommunication equipment or other electrical equipment where an unexpected power disruption could cause injuries, fatalities, serious business disruption or data loss. UPS units come in sizes ranging from units which will back up a single computer without monitor (around 200VA) to units which will power entire data centers or buildings (several megawatts).
Our customer specializes in ruggedized UPS systems designed for demanding remote or mobile applications for use in harsh physical and electrical environments worldwide. The subject 2500 VA UPS system, which has wide universal inputs and frequency tolerances, can operate in international power environments and be used in tracked and wheeled vehicles. Typical run time is 8.5 minutes. About the size of a smaller-than-average suitcase, the system weighs about 135 pounds.
The Vicor battery charger solution was designed using four 375 V Maxi DC-DC converters, each with a DC output of 54 V at 600 W. A 48 Vin Micro DC-DC converter provided 12 V at 100 W for auxiliary power. These converter modules are fully encapsulated using a proprietary spin fill process making them suitable for the most harsh environments. They can withstand temperatures from –10 to +100°C (operating) and –20 to +125°C (storage). The modules were subjected to the environmental testing requirements of MIL-STD-810, MIL-S-901, MIL-STD-202 and undergo 100% environmental stress screening.
Maxi Modules Used for UPS Retrofit for Guided-Missile Destroyers
The roles and characteristics of a naval destroyer have changed markedly since World War II. They are much larger — about the size of a WWII cruiser — and independent, no longer needing a destroyer tender. Their firepower is much more lethal than that of any cruiser. Now called guided-missile destroyers, they carry missiles — even with nuclear warheads — that can be launched against air, sea, or land targets. They still, however, retain their anti-submarine and fleet protection roles.
The Vicor customer is a unit of a very well-known company that is better known in the life science marketplace than the military. The application, part of a retrofit program for a guided missile destroyer, was for the modification of an uninterruptible power supply (UPS) for engine control. The original power supply was a discrete design, and one objective of the modification program was to simplify the design process by using component power devices. The use of military COTS components was a requirement.
Two Vicor Maxis were used; one input was 48 V with an output of 28 V. A second input was 28 V with an output of 5 V. The Maxi modules were particularly appealing because they utilize a proprietary spin-fill process to assure void-free encapsulation making them suitable for the harshest environments. M-grade modules permit operating temperatures from –55 to +100ºC. Such modules are subjected to the environmental testing requirements of MIL-STD-810, MIL-S-901, MIL-STD-202, and undergo100% environmental stress screening.